Shaping Uganda’s Steel Industry: Insights from Sanjay Awasthi-Chairman Tembo Steels Limited
In an exclusive interview, Sanjay Awasthi, CEO of Tembo Steels Uganda, shared insights into the company’s pivotal role in the Uganda steel industry. Since its inception in 2000, Tembo Steels has been a leader in steel manufacturing in Uganda, pioneering innovations like TMT bars production and lightweight structural steel. The company is the sole provider of primary steel production in the country, utilizing Directly Reduced Iron (DRI) to ensure high-quality products while setting benchmarks for purity and strength.
Awasthi highlighted Uganda’s steel industry trends, noting its transition from reliance on secondary steel production to a more advanced, value-added model. Despite challenges from foreign competition, such as Chinese imports, Tembo Steels has maintained its competitive edge by innovating and expanding its production capacities, including a soon-to-launch DRI plant.
Sustainability is at the heart of Tembo Steels’ operations, as it drives green steel practices in Uganda. The company has achieved a carbon emissions matrix close to 70%, far exceeding global averages. Awasthi emphasized the need for collective action in reducing CO2 emissions, especially as Uganda steel manufacturers strive to align with international sustainability standards.
In addition to its industrial achievements, Tembo Steels is deeply committed to corporate social responsibility in Uganda, contributing to healthcare and environmental initiatives. From producing oxygen during the COVID-19 crisis to conducting extensive plantation projects, the company underscores its dedication to community well-being.
Looking ahead, Awasthi envisions Tembo Steels setting global benchmarks in sustainable steel production, reinforcing its leadership in the Uganda steel market while continuing to innovate and support the country’s economic growth.
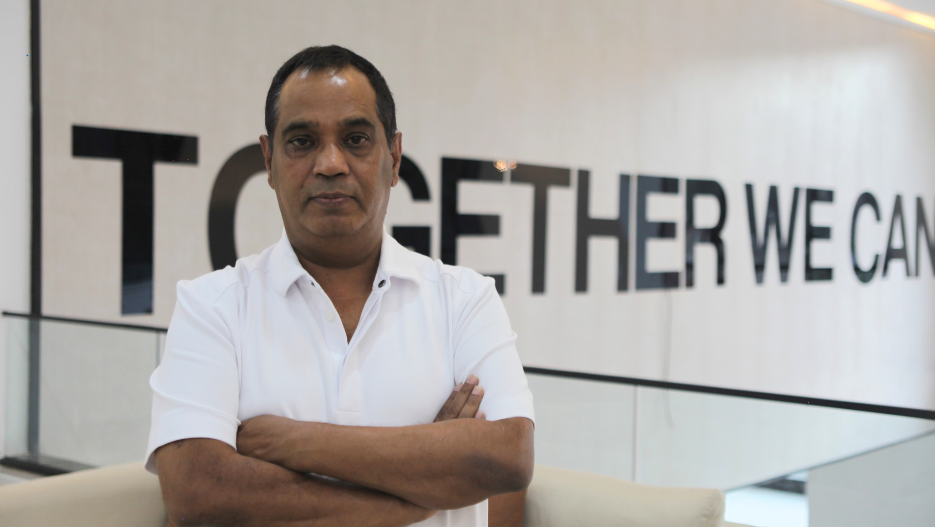
Could you please introduce yourself and give a brief overview of your company?
My name is Sanjay Awasthi, and I represent Tembo Steels Limited. Our journey began in 2000 when we pioneered the production of TMT bars in Uganda. TMT, which stands for thermomechanically treated bars, are high-strength, flexible bars that enable steel savings of around 15-20% in high-rise buildings due to their strength.
In 2008, we expanded into structural steel production in Uganda. We now operate two manufacturing units—one in Bukharaji and another in Lugazi itself. Uganda recently began producing Directly Reduced Iron (DRI), which serves as our main input material. One of our DRI plants, with a capacity of 100,000 tons per annum, has been operational since 2018, while a second plant with a 250,000-ton capacity is set to launch in November. Combined, these units will provide a capacity of 350,000 tons, making us the only primary steel producer in Uganda.
In addition to TMT bars for high rises and dams, we produce structural steel for fabrication, HRC for hot welded sheets, and wire rods, a facility we were the first to introduce in East Africa. With our expanded facility in Balaji, we now achieve a wire rod production capacity of 300,000 tons, structural steel capacity of 150,000 tons, and a crude steel capacity of approximately 600,000 tons.
In terms of product diversity, we lead the continent in the variety of combustors and substrates we produce—offering an unmatched range across Africa.
What is your view on the trends, challenges, and opportunities in Uganda?
The steel industry in Uganda is thriving, with close to a dozen steel plants operating. These plants are primarily in the secondary and tertiary sectors. Uganda’s total installed steel production capacity is nearly two and a half million tons. Primary steel production has just started, and currently, Tango Steels is the only company engaged in this segment. All other companies focus on secondary and tertiary steel production.
In secondary steel production, value addition ranges from 50% to 100%, with companies starting at different levels of value addition. Some begin at 50% and go to 100%, while others start at 30% and progress up to 70%. These varying levels of value addition create distinct segments within Uganda’s steel industry. Primary steel production, though new, is anticipated to mature over time.
Can you tell us more about your products and services, including what makes Tembo Steel unique and sets it apart from competitors?
We are the only primary steel producer in the country, which gives us an inherent advantage in steel purity. Primary steel production, using virgin iron ore, avoids residual elements found in scrap melting. These residual elements can weaken overall quality, affecting strength and ductility. Our position as the sole primary steel manufacturer ensures a superior product.
What key projects have you completed or are currently working on?
I would like to highlight a unique project we completed in 2004. In that year, we started converting cast iron into liquid low carbon steel for Africa. At that time, no other company in the world was undertaking this conversion. We identified a need for an alternative raw material in steel manufacturing, as the only available option was mild steel scrap. Many companies were melting mild steel scrap to produce structural steel profiles, TNT bars, and wire rods.
We recognized the opportunity to use cast iron, which was abundant, as a raw material. Although cast iron contains nearly 4% carbon, making it challenging to process, we saw its potential. We successfully developed a method to convert cast iron into liquid mild steel, which can be utilized in secondary steel making. This achievement positions Tembo Steel as the first converter in the world to transform cast iron into liquid low carbon steel.
Additionally, Tembo Steel is associated with other global benchmarks. We manufacture the lightest structural steel in the world, ensuring that structural profiles used in fabrication do not compromise strength and ductility. We optimized the design without sacrificing performance, allowing us to proudly claim our position as the manufacturer of lightweight structural steel section profiles globally.
You already addressed my question about a success story. Is there anything else you would like to highlight?
We are associated with lightest auto seed profiles. The lightest auto seed profiles are manufactured by Tembo Steel in Uganda since 2004. However, Chinese imports in the region have made our operations very difficult. The overall viability and economics were at a critical state in 2012 to 2013, prompting the need to introduce our product to compete with Chinese imports. We decided to produce the lightest auto seeds without compromising their strength. The product remains number one because we produce auto seeds through configurations that are highly effective.
We engage in various philanthropic activities, such as participating in cultural events directly related to cancer, charity, and patient support, including eye surgeries. We are involved in many projects through these cultural events. Our budget for this is close to $150,000 per annum, which supports our other initiatives. We also operate the largest oxygen facility in the country. During the COVID-19 pandemic, there was a scarcity of oxygen, which became essential for saving lives. This is where we contributed significantly. Additionally, we provided a brand new system that facilitated care during that time. We frequently supply hospital beds, targeting 500 beds annually. We also conduct extensive plantation projects in and around the hospital. We are fully committed to corporate social responsibility.
Where do you see yourself and Tembo Steel in the next three years?
We produce high-quality steel. When discussing steel quality, it is essential to consider efficiency and productivity, as these factors make life easier in today’s competitive market. To survive, we must be competitive, efficient, and productive. To achieve efficiency and productivity, we are committed to excellence in productivity analysis. So far, we have approached excellence in these areas. In terms of efficiency and productivity of our steel products, we are close to European standards.
Can you share your personal journey and leadership experience? What motivates you to wake up every day?
I am passionate about steel. This passion drives me and will continue to motivate me.
And leadership experience, is there anything you would like to share with us?
In my understanding, a leader must know the path, show the path, and then step away from the path. This is precisely what I practice.
Is there anything you would like to add?
Regarding green steel, there is a global awareness of the need to reduce carbon emissions. This is a pressing issue today. In the steel industry, primary steelmaking emits approximately 2.2 tons of CO2 per ton of steel produced. About 70% of total steel production comes from blast furnaces, which are the primary method of steelmaking. There is also a secondary process using scrap, but this has limitations due to availability and quantity.
To address the need for a greener future in steel production, the industry must contribute collectively. The total impact of the steel industry accounts for about 78% of emissions, and everyone must work towards a more sustainable tomorrow.
We are among the few companies globally that practice green steel production. We have achieved a carbon emissions matrix close to 70%, placing us in an elite category within the primary steel sector. The worldwide average for green steel production is approximately 40%, while Europe averages around 45% and the USA around 55%. Tembo Steel Uganda Ltd. has achieved a matrix close to 70%, which I consider phenomenal.
How can the Uganda manufacturing industry better promote sustainable practices, and what role does Tembo Steel play in driving that change?
Europe’s green steel market averages between 45% and 55%. For example, China produces around one billion tons of steel annually, accounting for 55% of the world’s total steel production. However, 90% of China’s steel is produced from blast furnaces, which are considered less sustainable. The global aim is to reduce emissions to around 400 kilograms of CO2 per ton of steel produced, while China’s average is about 2 tons.
As China develops, it is becoming more aware of the need for green steel practices. Currently, China’s total green index is around 1.8 to 2 tons. The global target for steel production was set at 2.45 tons of CO2 per ton produced by 2015, aiming for 450 kilograms of emissions by that time. At Tembo Steel, our average is close to 2.45 tons, which means we are ahead of schedule.
FAIR USE POLICY
This material (including media content) may not be published, broadcasted, rewritten, or redistributed. However, linking directly to the page (including the source, i.e. Marcopolis.net) is permitted and encouraged.